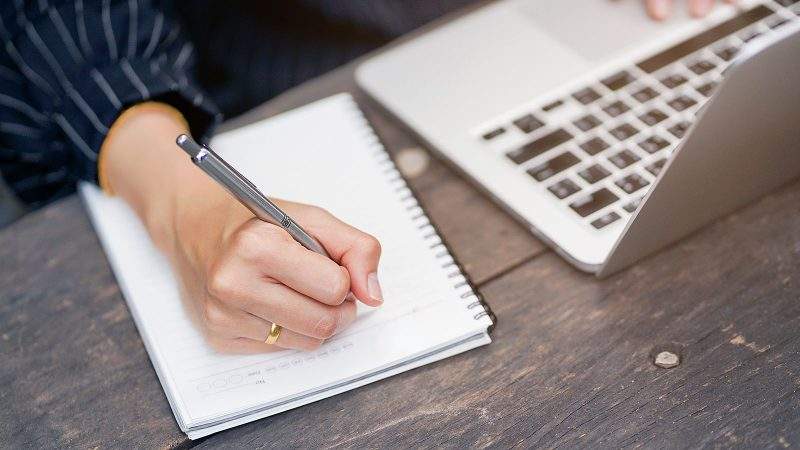
Introduction To Supply Chain Management And Logistics

Supply chain management is one of the processes of managing the raw material and production and ends at the delivery to the customers. In many companies, there are hundreds of supply chain decisions made on daily basis on how the development and manufacturing of products are moved and sold. The complexity of supply chain management depends on the size of the business and also on the nature of the business. It is obvious that if you have a large size of business then you have to deal with a large number of items manufactured and delivered on daily basis.
Supply chain management is a vast subject and demands a good amount of updated knowledge. Students who are studying supply chain management for logistics as their specialization had to deal with a variety of assignments. It becomes difficult for the supplies in management students to write a thesis at the end of the program. I always recommend students to get professional UK dissertation help if they want to complete their thesis according to the standards and requirements of the university.
What Are The Elements Of Supply Chain Management?
There are many elements involved throughout the supply chain management that are considered as basic factors. Let’s see these basic considerations one by one in order to get the right understanding of the supply chain management and logistics.
Customers
The supply chain management starts from the customers when they create a demand for a certain product and they decide to purchase a specific product offered by the company. The sale order comes in the process when the product has to be manufactured in the specific facility.
Planning
It is important to plan how much to produce and when to produce. Therefore, there are specific planning departments for every organization that see the demand for the product and plan the production accordingly. The planning department helps to fulfill the customer’s order and to manufacture the products. This allows the company to purchase the raw material according to the demand for the sale.
Purchasing
The purchasing department is involved to list down the raw material and services required by the production department so that they can complete the orders of the customers accordingly.
Inventory
Inventory includes the raw material that has been received from the suppliers and is checked for reliability and quality. Once it is checked, it is moved to the warehouse.
Production
Production is always based on planning. The raw material from the warehouse is moved to the production facility. At the production facility in these raw materials are used to manufacture the products according to the customer’s order and then sent to the warehouse for delivery purposes.
Transportation
Once the finished products come into the warehouse, then it is the duty of the shipping department to select the most effective and relevant shipment methods to deliver the product to the customers on the promised date.
What Is Logistics?
When we talk about the business and organizations, logistics is all about the management of the floor of things between the point of origin to the point of consumption so that the specific business and Organisation can meet the standards and requirements of the customers.
Physical item logistics includes the complete integration of production, packaging, inventory, warehousing, transportation, informational flow, and material handling. Many times people confuse in differentiating between logistics and supply chain management. However, it is now globally accepted that activities involved throughout Logistics are related to the distribution of the products throughout the organisation. If we see, the supply chain also includes procurement and manufacturing and it definitely has a broader perspective then logistics. You can just say that logistics is a small part of the supply chain management.
Supply chain management is a process where different enterprises including manufacturers, retailers, and suppliers working together to meet the requirements of the customers accordingly.
What Is Inbound Logistics?
Inbound logistics is all about managing the incoming flow of the resources that are required by the company to produce specific goods or to provide the relevant services. The inbound logistics activities include the relationship with the supplier while getting raw materials and negotiating the prices along with the quick delivery methods.
The optimisation of inbound logistics depends on the streamline of business operations. It is important to understand the full picture of the movement throughout the network to understand the functions of the network. If you want to optimise your inbound logistics, then it is important for you to understand everything starting from receiving products from the supplier to transporting the finished products to your facility and to distribute them effectively and efficiently. Third-party logistics is one of the best ways to do your business.
What Is Outbound Logistics?
The entire outbound logistics depends on two factors that are storage and transportation of the goods and services. It is important for the outbound Logistics manager to use the best and effective warehousing techniques in order to keep the finished goods safe and easily accessible. The movement of the products throughout the warehouse is much important and for such things, proper organisation is required. It is good if organisations have little products stored because use it is not giving any kind of advantages of keeping the high amount of products in the stores.
The job of the outbound Logistic manager is to balance the cost-saving of the organisation with customer demand. Transportation is also included in outbound logistics and is one of the most complex paths of outbound Logistics. Without transportation the logistics are nothing. It is difficult to select the most effective and cost-effective transportation method. Transportation methods should include the fastest and most effective modes of transportation. The most difficult thing is the fluctuation of the fuel cost along with many other fluctuating factors that are must be considered throughout outbound logistics.